What Steps Should You Take to Control Hazardous Substances at Work?
Each year, hazardous substances cause thousands of workers to become unwell. These illnesses include serious ones like skin cancer, asthma, and cancer. Employers must take preventative precautions to shield their staff from harmful chemicals.
For tips on how to take charge at work and lower the risk, keep reading!
1. Identify harmful substances in your workplace
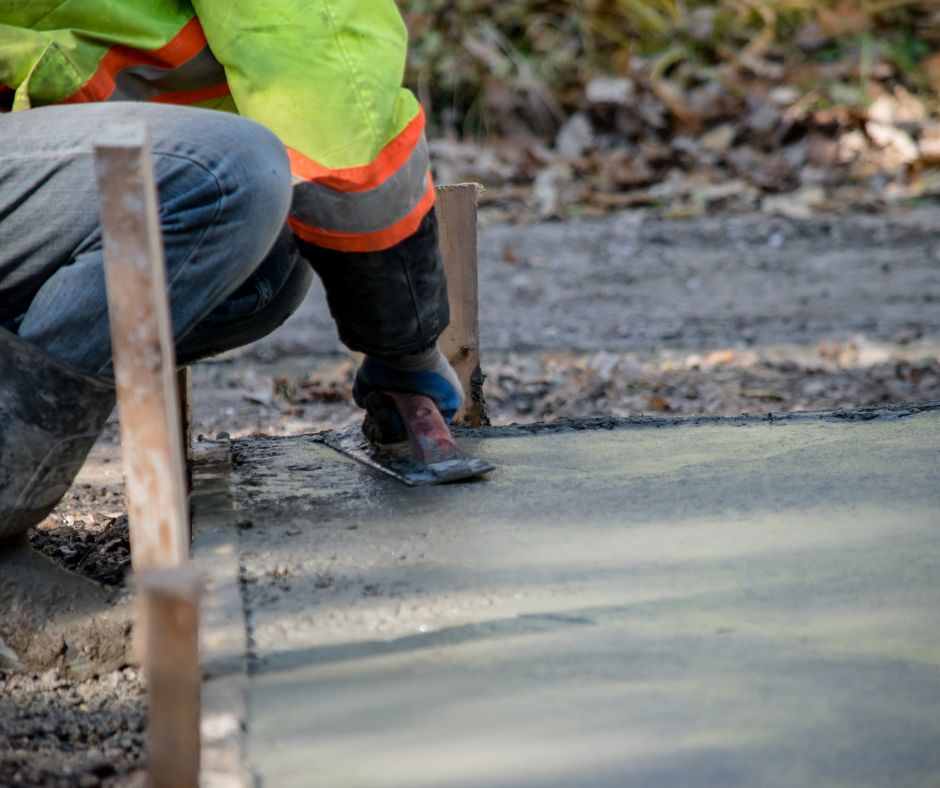
It is crucial to carefully assess all substances you work with, including those that might seem risk-free. Even common materials can be hazardous if used improperly; for instance, they may be combustible or cause respiratory problems when inhaled.
By checking any information that comes with a product, getting in touch with the supplier, doing some research in the trade press, or utilising the HSE website, you can find out if any compounds are dangerous.
2. Consider the task
Examine any tasks that use hazardous substances and consider the potential exposure your employees may face. Is it possible to alter the task so that the danger of exposure is eliminated or reduced?
3. Consider potential types of exposure
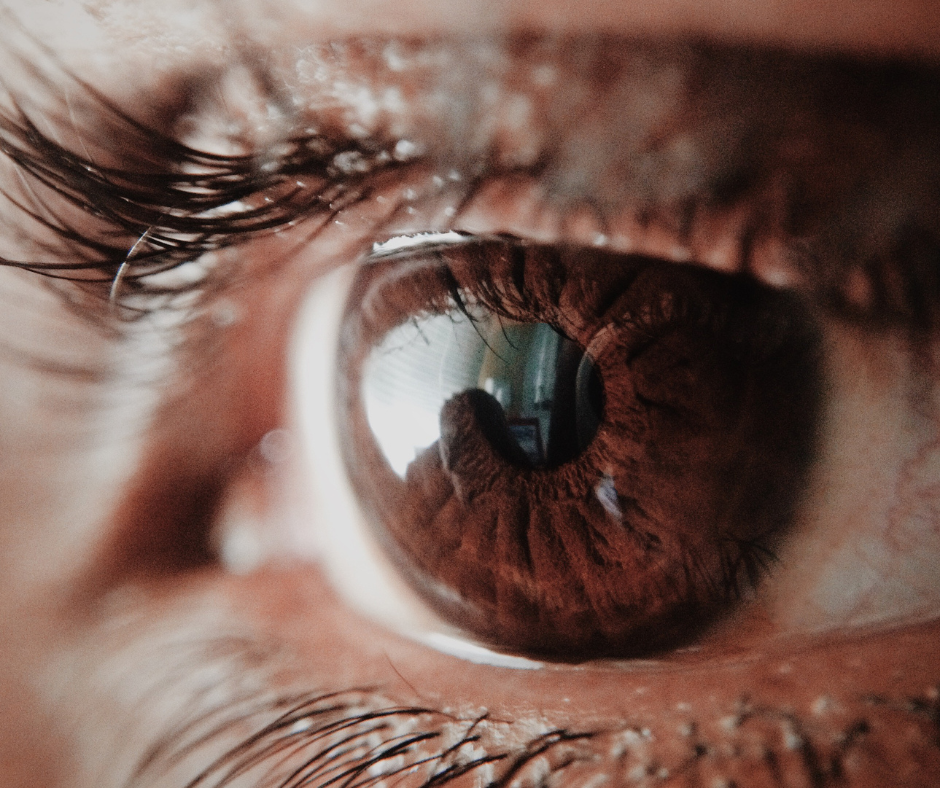
Workers may be exposed to hazardous substances in a variety of ways. These include:
- breathing in gases, fumes, mist or dust
- contact with the skin
- swallowing
- contact with the eyes
- skin puncture
Check chemicals to make sure you are aware of what forms are toxic and what exposure techniques are troublesome, because certain compounds may be safe in one form but dangerous in another.
4. Conduct risk assessments
Employers must evaluate the risk of exposure to their employees as per the Substances Hazardous to Health Regulations of 2002 and take appropriate steps to prevent or manage such risks. You need to know how employees might be exposed and how much they might potentially be exposed to in order to do a risk assessment. This will help you to decide what control measures you need to implement.
5. Choose control measures
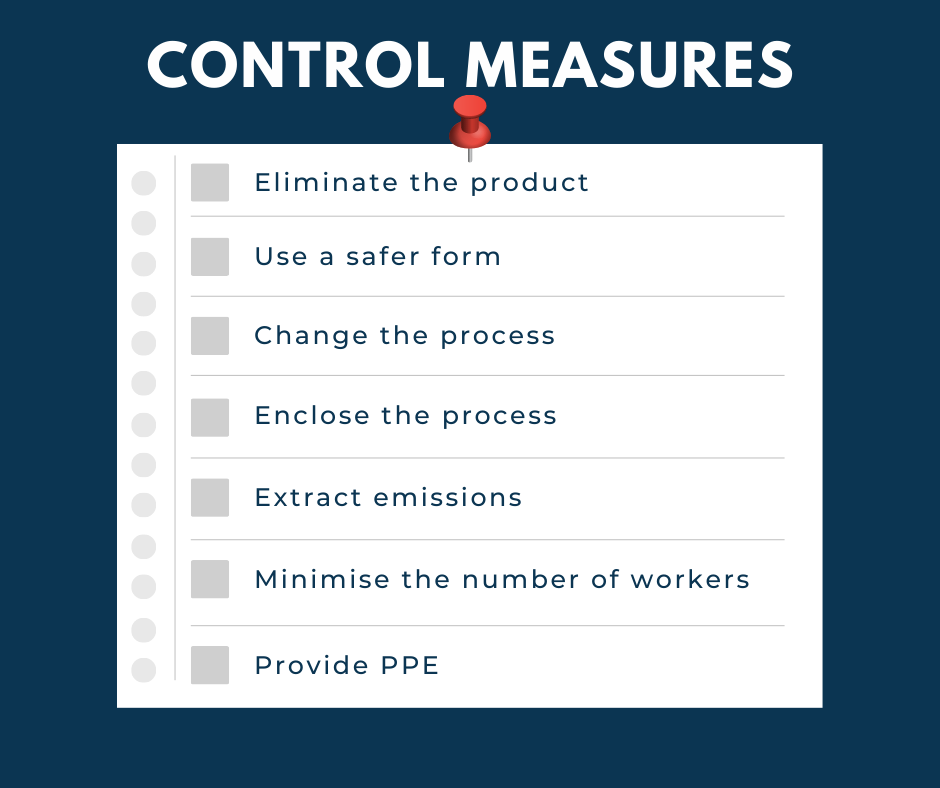
There are several techniques to reduce the danger of exposure to hazardous substances; in terms of importance, these are:
- Eliminate the use of a hazardous substance and replace with a safer one
- Use a safer form of the product
- Change the process so that less of the substances is emitted
- Enclose the process so that the product does not leave the area
- Extract substance emissions near the source
- Have as few workers involved as possible
- Provide PPE
Choose the control measures that suit the risk you have identified, following the above hierarchy.
6. Check and maintain your controls
To make sure that control measures are still functional and operating as intended, regular checks should be made.
When equipment is involved, such as exhaust ventilation or personal protective equipment, this is especially crucial. Both require routine inspection and upkeep because, if they stop functioning as they should, they cease to offer protection and may put workers in risk.
7. Ensure competence
Controls must be created, installed, maintained, and tested by someone who has the necessary skills. This includes
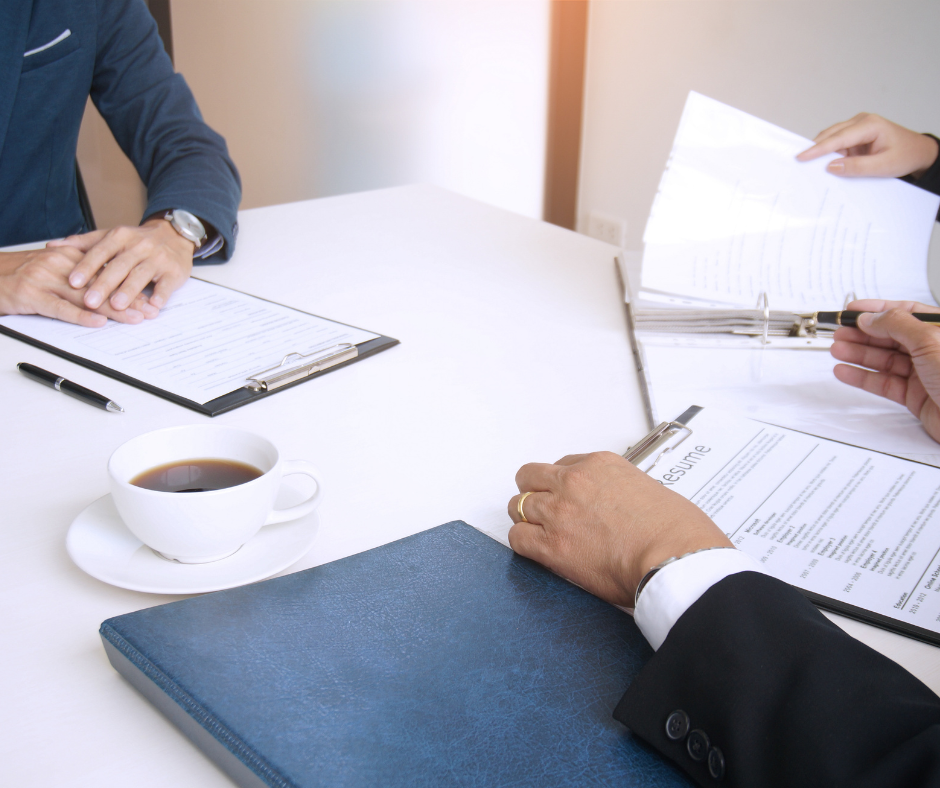
having the essential skills and qualifications, as well as knowledge and experience. Never hesitate to ask!
8. Provide sufficient training, instruction and information
You should give your employees:
- An appropriate explanation of the risks
- An understanding of how to utilise and appropriately check control measures
- Opportunity to conduct safe spill clean-up drills in practise
- For people who require respirators, face fitting and instruction
- Instructions on how to put on and take off safety gloves without touching your skin
9. Monitor exposure
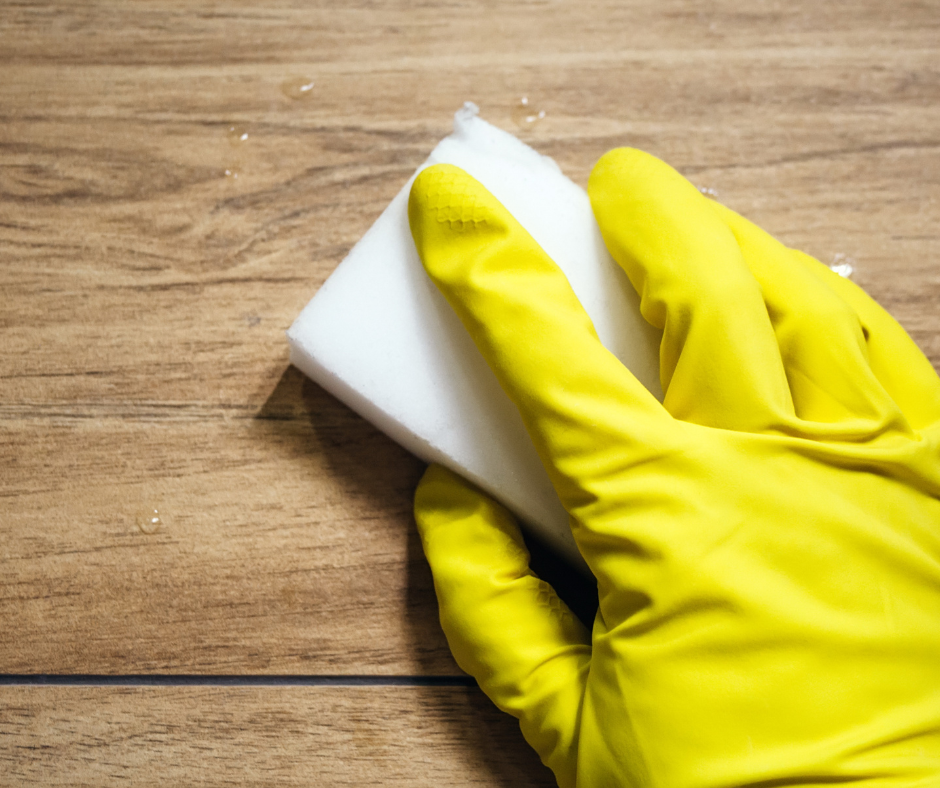
Monitoring is used to confirm that controls have been put in place and are adequate. To prevent the spread of contamination, this may entail sampling the air, collecting biological samples from employees, or wiping surfaces.
Exposure levels must not be higher than the “Workplace Exposure Limits” (WELs) set forth by HSE in order for controls to be considered satisfactory.
10. Carry out health checks
Health surveillance should be carried out in instances when:
- The substance in use is associated with a disease
- It is possible to detect the disease and reduce risk of further harm
- The disease is likely to appear due to conditions in the workplace
It is a regular assessment of aspects of a workers health, the results of which must be interpreted into actions to control exposure.